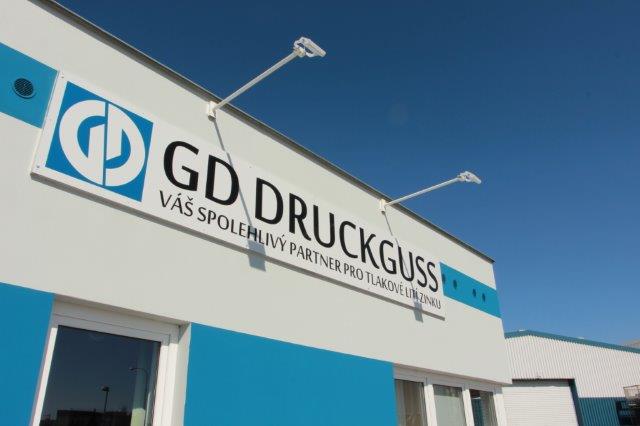
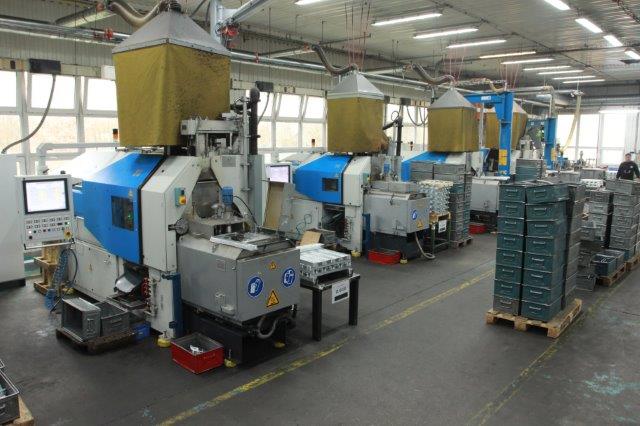
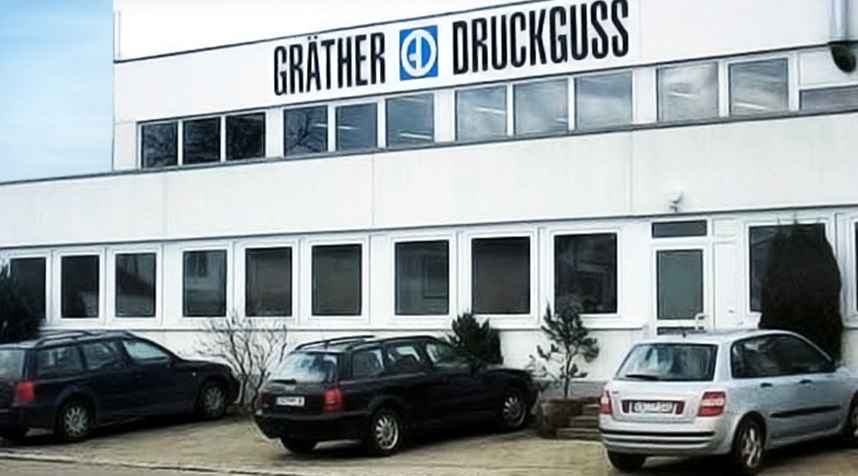
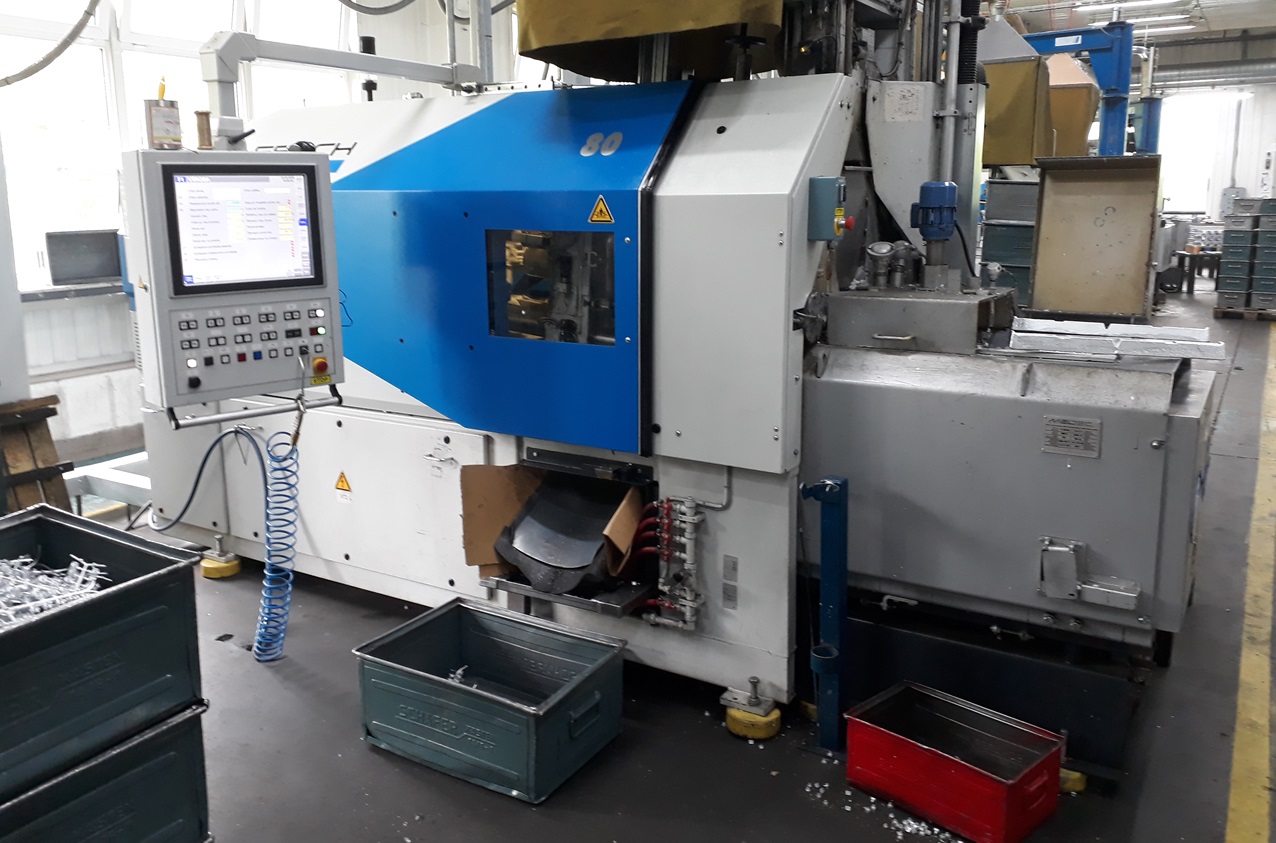
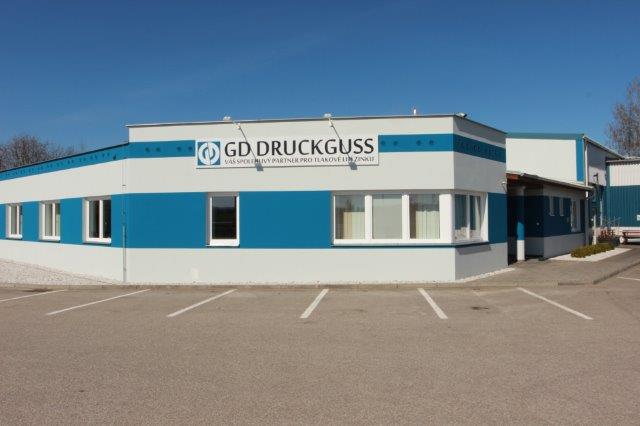
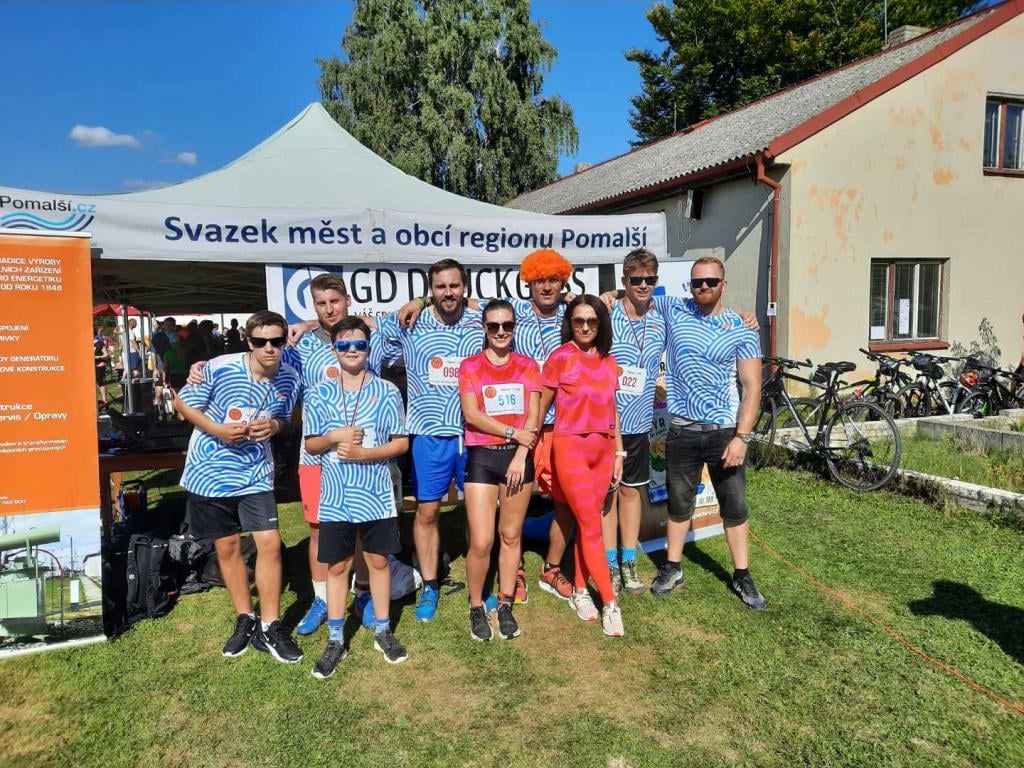
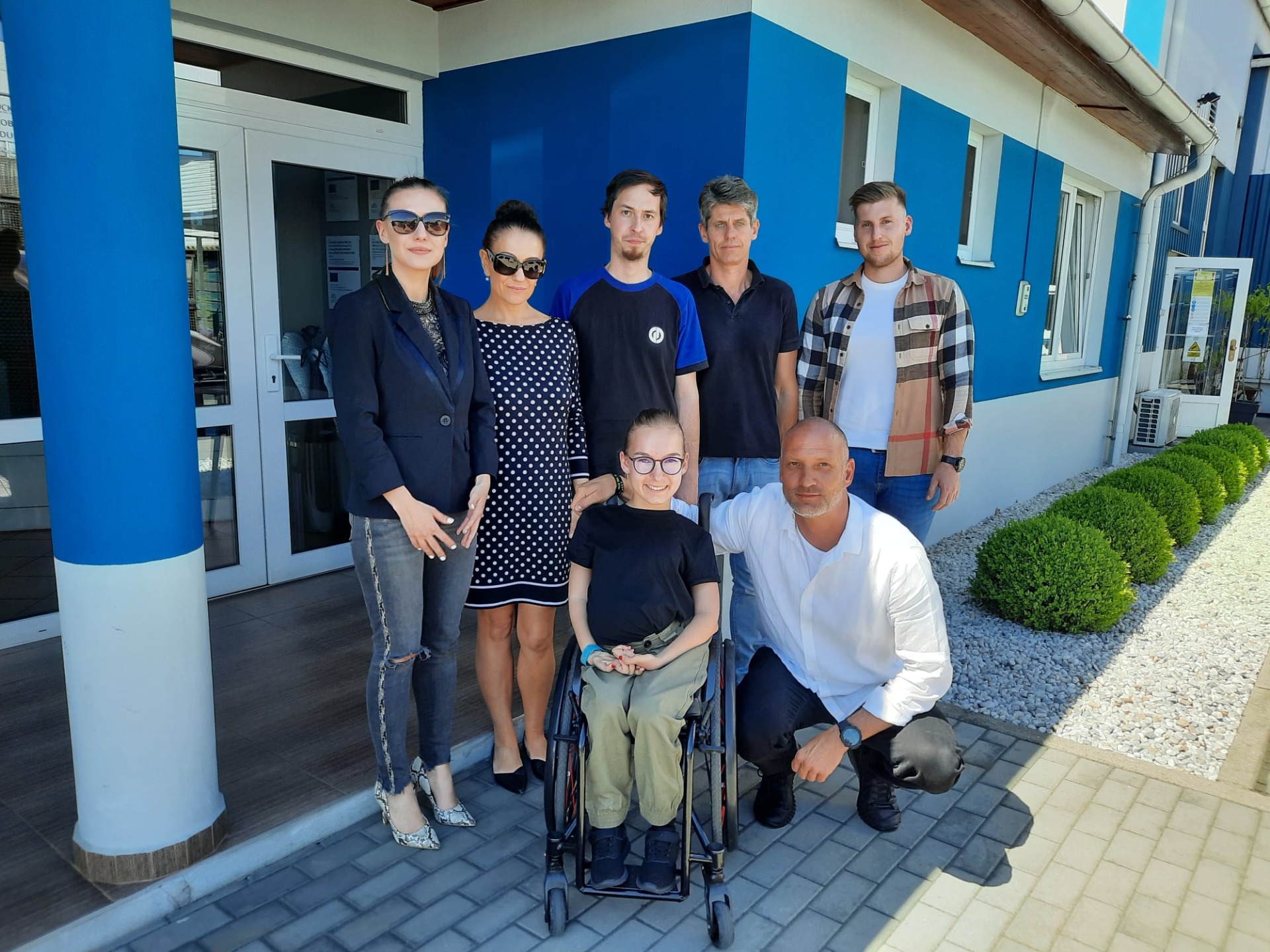
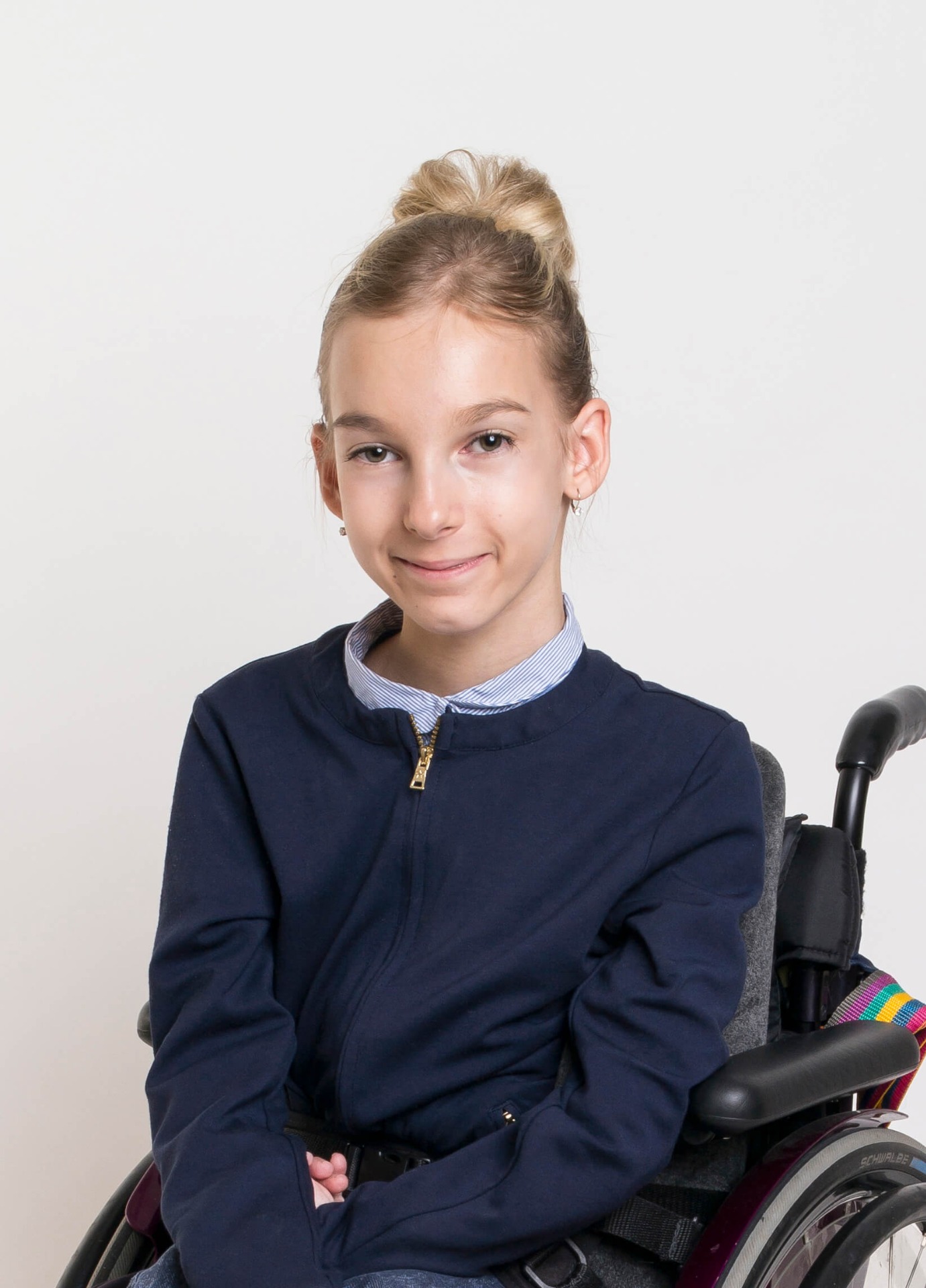

ABOUT US
Our core activity is the production of zinc alloy castings using die casting technology. We produce castings weighing between 5 and 750 grams under pressures of 5 to 80 tonnes. Both small product series in the range of thousands of items and mass production for multinational corporations are within our capabilities.
Our family-run company places maximum emphasis on customer satisfaction, flexibility, quality, and open and direct communication when addressing the needs and requirements of our customers.
All production processes are subject to the standards under ISO 9001:2016 and ISO 14001:2016 certification.
STRATEGIC COMPANY MILESTONES
In 1991, Erich Gräther founded the GRÄTHER-DRUCKGUSS company, benefiting from his education and apprenticeship in the field of toolmaking and his long-term experience as a casting die design engineer. Production began in rented manufacturing premises in Donaueschingen. Thanks to Mr Gräther's technical and business skills, the company enjoyed stable growth and moved into a new production hall in Hüfingen in 1996. In response to increased customer demand and in order to maintain the company competitiveness, construction of new premises in Vodňany began in 2000, thus beginning the new construction and shaping of the company's future development.
- 1991 - company establishment by Erich Gräther
- 1995 - the family of the current owner, Iveta Boskov, initiates cooperation with the Gräther company
- 1996 - relocation to larger premises in Hüfingen in the German state of Baden-Württemberg
- 2000 - Ms Boskov becomes the managing director of the newly founded Czech subsidiary Gräther-Tlakové lití s.r.o., working on the project to build a new production hall on the company-owned land; the project is completed in December 2002
- 2006 - the manufacturing facility in Vodňany is expanded with the addition of a new separation hall
- 2008 - Ms Boskov and her family purchase a business share in both the German and Czech branch of the company from Mr Gräther
- 2014 - construction of a new warehousing and assembly hall in the Czech Republic with an approximate size of 1,000 m2
- 2016 - relocation of the entire production programme and technology to the Czech Republic, and closure of the German branch in Hüfingen
- 2017 - new corporate structure and new business name GD Druckguss
- 2021 - purchased land for construction of new technological operations and company development
- 2022 - preparation for addition of operations in the existing facility on Radomilická Street (construction scheduled to start in Q1 2023)
40 employees are currently a part of the existing business and production structure of the company. Our priority remains meeting goals for maintaining quality standards, flexibility and, thereby, customer satisfaction.
STRATEGIC COMPANY MILESTONES
Římov Run
As part of our regular charity activities, we decided to support the 5th Římov Run for Smile charity event, held on 15 June 2019.
This time, we not only supported the event with a financial donation, but also formed a team of colleagues to participate in the Římov Run for the smiles of children who face several challenges in their lives. This jubilee year was namely dedicated to sixteen-year-old Bára Sedláčková, six-year-old Karolínka from Borotín and four-year-old Martínek from Střížov. The proceeds from this sports afternoon at least partly helped the children in their determination to improve their lives. Many thanks to the enthusiastic promoters of this project.
The 6th annual Římov Run for Smile was held on 4 September 2021, which our company not only supported with a financial donation, but also took an active part in.
It was not only a record-breaking year in terms of the 400 base registered runners, but mainly the record-breaking total of CZK 330,000 that was raised thanks to sponsors, runners and visitors. The financial support was split among the family of nine-year-old Anežka from Zliv, who was diagnosed with a rare motion-inhibiting genetic disorder, and the Modrá pomněnka non-profit organisation that provides psychological and social assistance to families of incurable patients.
We could not miss the charity Římov Run for Smile that has become an affair of our hearts in 2022 either. In addition to the financial support, we also took an active part in this charity event as runners. The 7th annual run held on 18 June 2022 noted a new total record that exceeded CZK 400,000. The proceeds from this year's event were namely provided to Adélka Kačenová, Adélka Křiváčková and the Arpida Centre. Many thanks to the visitors and enthusiastic runners, but mainly to all sponsors.
Bára Sedláčková
In summer of 2021, Bára Sedláčková, a talented handicapped artist who we met in 2019 on the occasion of the 5th annual Římov Run for Smile, visited us with her mum. We keep track of and support Bára's work.
Bára paints with her mouth as her legs and arms were paralysed by disease twelve years ago, confining her to a wheelchair. In order to show her creative talent, she has gradually mastered her own visual style called Pusopis (mouth-writing), and her paintings are so successful that she has already had eleven individual exhibitions all over the Czech Republic since 2013. (for details go to www.pusopis.cz)
Bára's story, courage and fighting spirit gripped us so much that, based on another meeting with her and her mum, we agreed to provide periodic financial support that should help Bára and her family make their day-to-day life easier.
Support of Vodňany Library
In 2020, we financially supported reconstruction of the children's department of the local library in Vodňany. This enabled the library to be furnished with hanging chairs and sensorimotor mats. We wish the little readers to have great experiences when discovering the book world of fantasy, adventure and fun.
We supported the same library, newly called Gelastus Vodňanský Library, again in 2022 as a part of the yard refurbishment project that will, once finished, certainly be a dignified area for various gatherings or cultural events not only related to the library. Namely, we supported the 2nd stage of the "Help Us Finish the U Koníčka Yard" project with a donation. We are very happy to participate in helping establish such a place become very interesting in the future.